Using artificial intelligence to locate objects in industrial settings.
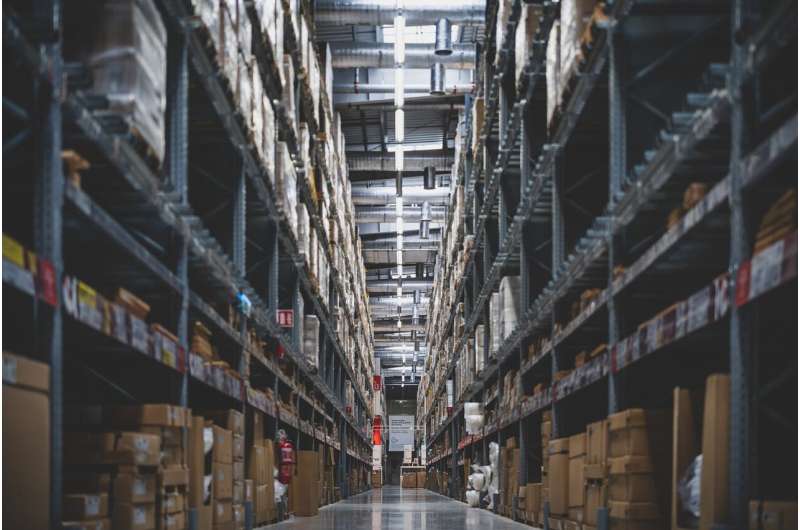
Indoor positioning is a big part of the industrial sector's digital transformation. From logistics to health care, tracking objects, assets and people accurately and cheaply could save companies time, money, and resources.
Professor Xavier Vilajosana coordinates the university's participation in a new European project that's working on indoor environments.
With DUNE, deep learning is combined with distributed computing, which takes advantage of both cloud and edge computing. These are computer architectures that operate on remote servers and close to where the data is generated. The goal is to create a flexible system that can adapt to different use cases.
"There are lots of technological approaches today that use radio signals to get the relative positions between objects. Technology is so vast and there are so many ways to use it, with so many budgets and environments, that we have to build a powerful framework for managing location data in real time from all kinds of technologies," said Xavier Vilajosana. "At the same time, it's flexible enough to meet multiple industrial needs and economically affordable," he explained.
Using deep learning to help with positioning
By analyzing the point of view of the receiver, indoor asset location deduces what direction the signals emitted by objects are coming from and estimates their position. A major challenge with this technology is the wide margin of error caused by obstacles between the transmitter and receiver, especially in industrial environments, and multipath propagation. Radio waves can travel by more than one path and reach the antenna at different times with multipath propagation.
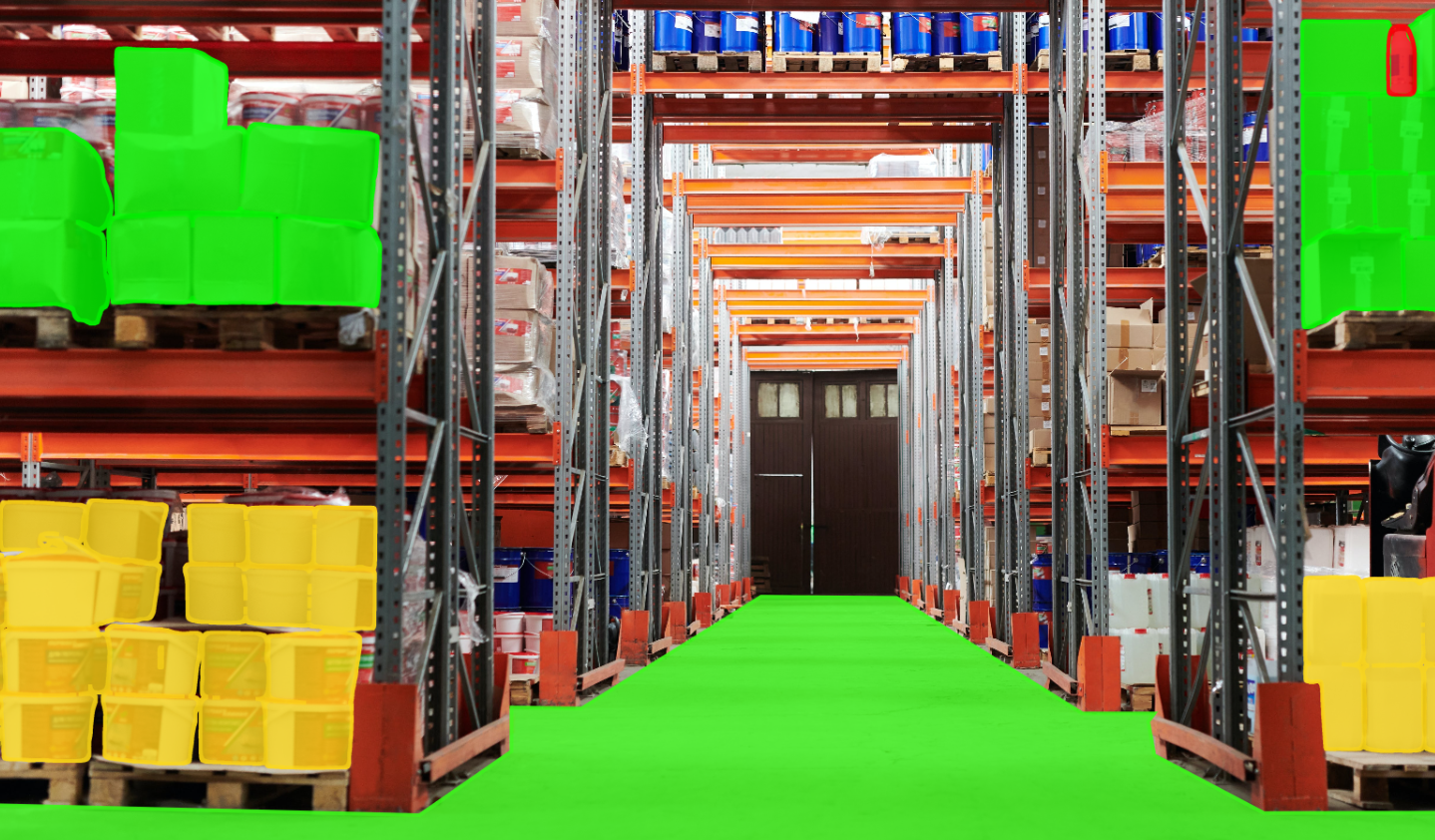
Due to this, signal processing is crucial-without it, ambiguities arise, leading to errors in object placement. The DUNE system uses deep learning techniques at various stages of the location process to handle this challenge. A deep learning algorithm learns from input and uses that knowledge to make inferences based on new information. "Different approaches are used to process the data, like deep learning, which trains position estimates to find the best location for the tracked objects," said the researcher.
Strategies for distributed computing
This project will also use edge and cloud computing. As a result, cloud computing processes won't take as long because the computation will be distributed in different nodes closer to the data source. This will cut down on servers' response times and bandwidth, and increase data security.
The system is completely distributed, and consists of different sensors and location technologies. In order to estimate their individual positions, these devices create raw data. Initially, data is processed at the "far-edge," which is near the antennas.
Real-time data
A locator's antennas pick up radio signals from sensors attached to objects or people to track. In order to calculate the angle that defines the direction of the signal, these data have to be transformed. According to Xavier Vilajosana, "in a perfect world, this transformation depends on the distance between the antennas and the radio frequency (wavelength).
Deep learning can be a very valuable tool for estimating object positions accurately when addressing these problems, he said.
In order to improve performance, other "edge" devices process and aggregate data in real-time. Here's another filtering step to improve signal translation and to incorporate different technologies, like deep learning.
A cloud-based infrastructure
These edge devices send real-time positions to a cloud infrastructure that's connected to the factory or warehouse's info systems. Using artificial intelligence in the cloud, you can fix, improve, classify, detect anomalies, and optimize operations.
Cloud infrastructure displays and tracks objects, and connects and interconnects them with other subsystems, like inventory in factories and warehouses.
Bench for large-scale testing
Throughout the 12-month project, this technological proposal will be evaluated in different scenarios, and the results will be compared to other current technology solutions. The research group will start with tests in its own lab, and then large-scale tests will be done in a building designed just for this type of experiment, with 1,000 square meters and the capacity to evaluate a bunch of different technologies.
Comments ()